2017/03/10
フル・スクラッチ ボイラー 形式1060
ボイラーとランボードを半田付けする前に、1.0 X 0.2mmの帯板を巻いてボイラーバンドを表現した。
この時、火室の位置決めのために作った冶具が大いに役に立った。
つまり、ボイラーを冶具に嵌め込んだ上で、冶具の火室部分をバイスに咥えると、バイスの重みでボイラーの保持が難なく出来る。そうすると両手が使えるので、左手に持ったピンセットで帯板を抑え、右手の半田鏝で半田を流すことが出来ると云った按配。
これまでは、この様な冶具を作ったことはなく、その際、ボイラーバンドをどの様にして巻いたか記憶が定かではないが、その時よりも遥かに簡単に工作が出来たことだけは確かだと思う。
と云う訳で、余勢をかって、1.2mmのパイプの中に0.5mmの角線を通して洗口栓もそれらしく作った。
2017/03/09
フル・スクラッチ 上回り 形式1060
ランボードを0.5mmの真鍮板から切り抜いた。尚、ランボードとキャブの床板は、この形式1060の原型である形式6120の写真から判断して、一枚板にした。
又、火室の後部からキャブ下に延びる部分、及び、キャブの床が一段下がる部分は1mmにした。
これらを半田付けして、ボイラーと仮組してみたのが写真。
本来なら、火室部分と延長部分がピタリと隙間ない状態にならなければならないが、やはり、隙間が・・・・・・(涙)
この形式1060のスクラッチにあたっては、これまででは考えられない程慎重かつ丁寧に工作を進めて来た筈なのに、何故この様な結果になってしまうのだろうか?
2017/02/25
フル・スクラッチ 上回り 形式1060
果たして、上手く位置決めが出来るか心配だったが、心配だからと云って手を拱いて見ている訳にも行かず、兎に角、やって見た。
左右の高さが違うなど何度か失敗したが、何とか半田付けを終了させることが出来た。
火室の側板のボイラーとの接合部分は、予めRを付けているが、それでも段差が目に付くので、半田を盛って整形した。
こうして写真に撮ると、半田の盛り方に粗が見えるが、組み立ててしまえば目に付く部分ではないので、このまゝ先に進むことにする。
2017/02/23
未分類
ボイラーに火室を設置する段になって、良い方法が見付からず、暫しの間工作が滞っていた。
と云うのは、当初、ボイラー部分は真鍮板を曲げ、火室部分はボイラーの下部を曲げずに下に伸ばして表現する積りでいた。所が、実際にはボイラー部分はパイプを利用することに工作方法を変えたので、火室部分は後付けするしかなくなっていた。
そして、火室の横板を切り抜き曲げ加工を終わった所で、この板をボイラーのパイプに半田付けする際の位置決めをどうすれば良いのか分からず、気が付けば2月ももう終わり・・・・。
先ず、火室の幅決めをどうするか?
この蒸気の火室は、実機ではフレームの内側に落ち込んでいる筈だが、模型的にはギア・ケースやイコライザー等があるので、とてもフレームの内側にはその余裕がない。そこで、陰になっているので目立たないことを良いことに、火室の幅をフレームの外側と同じ幅にしている。
フレームの幅は9.8mm、火室の側板は0.4mmなので、幅が9mmの角棒を側板でサンドイッチにすれば、火室幅は決まる。
次に角棒の固定方法はどうするか?
汽笛の取り付け用に開けた穴を利用して、角棒をネジ止めする方法等考えたが、ボイラーの内径にピッタリの丸棒を削り出し、その丸棒に角棒を接着する方が正確な位置決めが出来るのではないか?
早速、工作に掛かり作って見たのが写真の冶具。
工作と云っても、工作らしいことをしたのは丸棒部分だけで、ここは、端材をML-210で削り出し、角棒部分は9mm角のラワン材を利用した。
果たして、これで上手く行くか?
上手く行って欲しい!!!
2017/02/05
フル・スクラッチ ボイラー 形式1060
念のため食塩水に付けたまゝにしていたボイラーを取り出して、ドリルが折れた個所をチェックすると、まだ何やら黒いものが残っている。そこで、改めて食塩水を作り直し、更にもう一日浸けていた。
そして、もう溶けてなくなった筈と思って、翌日ステンレスのコップを除くと赤錆が見えない。おかしいなぁと思い、再度折れた個所を25倍のピークルーペで見ても、やはり黒いものが・・・・・。
都合3日間も海水浴をさせていたのに、溶けないことがあるのだろうか?
少々、怖かったが恐る恐るピンバイスに咥えた0.6mmのドリルで抉る様にしてみた所、黒いものは刃の溶けカスだった様で、何の抵抗も感じられない。そこで、穴開け作業に移って、無事貫通。
0.5mmの方も同じで問題なく終了させることが出来た。
次の作業は、ボイラーの終端側の処理。
この形式1060のキャブ内にあるボイラーの終端は、垂直に切れておらず、僅かに斜めになっている。当初は、何も考えずに当然の様に垂直に切れている図面を描いていたが、蒸気機関車形式図集Iで少し斜めになっている図を見た以上無視する訳に行かず、それに倣って斜めにすることに変更した。
図面では簡単に斜めに切ることは出来たが、実際に正確に切断するのは少々所か、かなりの難題。正に絵に描いた餅状態。
工作は、出来ればフライス盤を使いたいが、良い素材の固定方法が思い付かず、時間ばかり経っていた。そんな時、フト、材料のパイプをバイスに咥え、そのバイスを更に別のバイスで咥えて角度を付けるのはどうかと思い付いた。
で、早速試して見ると、案外、上手く行きそう。
失敗するのが怖かったが、やらなければ先に進めない。
バイスにパイプを咥えるにも、余りきつく締めるとパイプが変形することもあり得るので、レンチを使わずに手で締めたので、切削の途中でパイプが動いてしまうこともある。そうなっては、元も子もなくなるので、切込み量を0.1mm以下にして、少しずつやって・・・・・・。
何とか、上手く切断出来た(写真では、終端の斜めになった切断面が良く分からないが・・・)
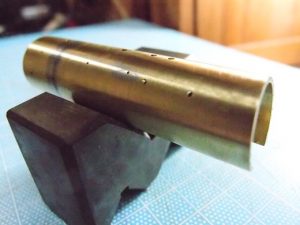
« 古い記事
新しい記事 »