※ カテゴリー別アーカイブ:ボイラー ※
2020/02/15
フル・スクラッチ ボイラー 上回り 形式1060
型式1060の側面には、後部と側面に設置された給水タンクを連結している太いパイプが走っている。手持ちの資料ではその太さの記載がないので、写真から適当に判断して、1.5mmの真鍮線を使うことにした。
この真鍮線を、それらしく曲げ加工をしなければならないのだが、そのために先ずジグを作った。
そして、工作に入ったのだが、思いの外真鍮線が硬くて上手く曲がってくれない。これまでの経験で、径1mmの真鍮線の曲げ加工はそれ程苦労することもなかったので、安易に考えていた。所が、1.5mmは硬い硬い。たった0.5mm太くなっただけで、こんなにも違うのかと驚かされた。
そこで、曲げる個所を部分的にナマしてみようと一旦は思った。しかし、ナマした上で曲げると加工そのものは容易になるが、出来上がりにシャープさを欠く様な印象だった様な記憶がある。
仕方がないので、小生の得意とする力技で数本作り、出来の良いものを採用することにした。
次いで、フランジ。分割されている連通管を連結するためのフランジの工作に入った。
これも資料の写真から適当にサイズを決め、中心に連通管が通る1.5mmの穴を空けた3m径の円盤に、固定するためのボルト用の0.4mmの穴を8個空けた。
実は、この工作があったので、簡易割り出し器を先ず作ることにした(左の写真はこの簡易割り出し器を使ってボルト用の0.4mmの穴を空けている所)。
フランジの様な円盤状の物を作る場合、小生は所定の厚みの真鍮片を丸棒の半田付けした上で、ML-210を使って所定の径にまで切削する方法を採っていた。
今回も当然同じ手法で工作に入ったのだが、直径3mm近くまで削り込んだ所で、丸棒から外れて切子の中に飛んで行ってしまうことが続いた。恐らく、直径3mmともなると接着面がかなり小さくなるので、切削する際の抵抗に負けてしまうのが原因だろう。1回の切込み量を少なくするか、バイトの切れ味を良くするかで解決出来ると思うが、今回は所定の穴を空けた3mmの丸棒を、所定の厚さに輪切りにする方法を採った。
左の写真は、力技で曲げて作った連通管とフランジ。
連通管は位置決め用の穴に通しただけの仮置き状態。又、フランジは予備を含めて5個作り、0.4mmの真鍮線を通しただけの状態で、この後、ボルトを表現すべく高さを削り揃えた上で、連通管に通して半田付けすることになる。
と云う訳で、連通管はパーツとしてはほゞ完了したが、これをどのタイミングで車体に固定するか、決め兼ねている。と云うのは、ランボードの下からキャブの下に掛けてブレーキ用の配管がウネウネと通っているので、順序を間違えると・・・・・・。
2017/04/20
フル・スクラッチ ボイラー 上回り 形式1060
皆様のお蔭で小径モーターが手に入り、何とか後戻りをせずに済みそうなので一安心。
と云う訳で、工作を再開。
本当なら、失敗した側板の作り直しに着手しなければ・・・。
と思ったが、側板に掛かる前に、作り直しをしなければならなくなった時のことを考えて、一部バラシていたボイラー部分を組み立てし直し、ついでにキャブの妻板を仮止めした。
と云うのも、ボイラーとランボードのセンターがずれている様な気がしてならなかったので、それを確認する意味で、煙突の一部と妻板を仮止めして見たもの。幸い、ずれておらず、ホッと胸をなで下ろした次第。
2017/03/27
フル・スクラッチ ボイラー 形式1060
面一にする筈の火室側板に出来てしまった僅かな段差については、目を瞑って先に進もうと思っていたのだが、試みに作り置いたキャブの前部妻板をボイラーに嵌めてみた所、やはりほんの少しセンターがズレてしまっている。
原因は、ボイラーがランボードの中央に位置していないためで、これは火室側板に段差が生じたことが起因している。
つまり、火室の段差 ⇒ ボイラーとランボードのズレ ⇒ 前部妻板のズレ
と云う3段論法が成立しそう・・・・・。
このズレは、陰になって目立ち難い火室部分に比べて、目に付き易いので、修正する必要があるが、そのためには火室側板の段差をなくす必要がある。と云う訳で、已む無く一旦バラシて半田付けのし直しをすることにした。
そして、改めて半田付けをしようとしている最中に、ボイラーのバックプレートをこの段階で半田付けしておかなければならないことに気が付いた。
バックプレートはWeast Japan Incのロストワックスの米国型パーツを使うことにしていたが、当然のことながら、この形式1060用に作られている訳ではない。と云っても、実機ではどの様になっているか資料もないし、仮に資料があっても自作出来る代物ではない。そこで、それらしければ良いと考えたのだが、それでも、ボイラーの外径に合わせる加工は最低限必要となる。その加工のためには、余計な床板などがない方が工作がし易いと云うことに気が付いたのは、怪我の功名と云う訳。
実際に行った加工の手順は、
1)バックプレートをボイラーに瞬間接着剤で固定し
2)ボイラーの外周に沿って罫書き
3)一旦、熱を加えてボイラーから外した上で
4)罫書き線に沿って大まかに切り出し(実際には、ヤスリでの切削)
5)ボイラーに半田付けの後
6)ボイラーの外周に合わせてヤスリで整えた。
尚、1)から4)までの手順については、切削しなければならない面積が大きかったので、ボイラーに固定されていない状態で加工する方がやり易いと考え、敢えて行ったもの。
この加工に当たっては、バックプレートに表現されているレバーやコックなどの細かいパーツを潰さない様にするのが大変で、色々と気を使った筈だが、結局、潰してしまったものがある。と云っても、極々小さなもので、パッと見には分からない程のものなので、まぁ、これで良しとしようと思う。
その後、改めて火室側板の半田付け等を行ったが、これが中々上手く行かず、何度やり直しをしたことか。
慎重に位置決めをした上で、半田付けをし、上手く行ったかと思いボイラーを突き合わせてみるとズレていたり、ズレがなくなったと喜んで妻板を嵌めてみるとセンターに合っていなかったり・・・・・・。
今日一日、この半田付けで費やしてしまったが、何とか、妥協出来る所まで来た。
2017/03/10
フル・スクラッチ ボイラー 形式1060
ボイラーとランボードを半田付けする前に、1.0 X 0.2mmの帯板を巻いてボイラーバンドを表現した。
この時、火室の位置決めのために作った冶具が大いに役に立った。
つまり、ボイラーを冶具に嵌め込んだ上で、冶具の火室部分をバイスに咥えると、バイスの重みでボイラーの保持が難なく出来る。そうすると両手が使えるので、左手に持ったピンセットで帯板を抑え、右手の半田鏝で半田を流すことが出来ると云った按配。
これまでは、この様な冶具を作ったことはなく、その際、ボイラーバンドをどの様にして巻いたか記憶が定かではないが、その時よりも遥かに簡単に工作が出来たことだけは確かだと思う。
と云う訳で、余勢をかって、1.2mmのパイプの中に0.5mmの角線を通して洗口栓もそれらしく作った。
2017/02/05
フル・スクラッチ ボイラー 形式1060
念のため食塩水に付けたまゝにしていたボイラーを取り出して、ドリルが折れた個所をチェックすると、まだ何やら黒いものが残っている。そこで、改めて食塩水を作り直し、更にもう一日浸けていた。
そして、もう溶けてなくなった筈と思って、翌日ステンレスのコップを除くと赤錆が見えない。おかしいなぁと思い、再度折れた個所を25倍のピークルーペで見ても、やはり黒いものが・・・・・。
都合3日間も海水浴をさせていたのに、溶けないことがあるのだろうか?
少々、怖かったが恐る恐るピンバイスに咥えた0.6mmのドリルで抉る様にしてみた所、黒いものは刃の溶けカスだった様で、何の抵抗も感じられない。そこで、穴開け作業に移って、無事貫通。
0.5mmの方も同じで問題なく終了させることが出来た。
次の作業は、ボイラーの終端側の処理。
この形式1060のキャブ内にあるボイラーの終端は、垂直に切れておらず、僅かに斜めになっている。当初は、何も考えずに当然の様に垂直に切れている図面を描いていたが、蒸気機関車形式図集Iで少し斜めになっている図を見た以上無視する訳に行かず、それに倣って斜めにすることに変更した。
図面では簡単に斜めに切ることは出来たが、実際に正確に切断するのは少々所か、かなりの難題。正に絵に描いた餅状態。
工作は、出来ればフライス盤を使いたいが、良い素材の固定方法が思い付かず、時間ばかり経っていた。そんな時、フト、材料のパイプをバイスに咥え、そのバイスを更に別のバイスで咥えて角度を付けるのはどうかと思い付いた。
で、早速試して見ると、案外、上手く行きそう。
失敗するのが怖かったが、やらなければ先に進めない。
バイスにパイプを咥えるにも、余りきつく締めるとパイプが変形することもあり得るので、レンチを使わずに手で締めたので、切削の途中でパイプが動いてしまうこともある。そうなっては、元も子もなくなるので、切込み量を0.1mm以下にして、少しずつやって・・・・・・。
何とか、上手く切断出来た(写真では、終端の斜めになった切断面が良く分からないが・・・)
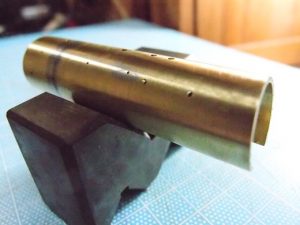
« 古い記事