※ カテゴリー別アーカイブ:フル・スクラッチ ※
2017/03/09
フル・スクラッチ 上回り 形式1060
ランボードを0.5mmの真鍮板から切り抜いた。尚、ランボードとキャブの床板は、この形式1060の原型である形式6120の写真から判断して、一枚板にした。
又、火室の後部からキャブ下に延びる部分、及び、キャブの床が一段下がる部分は1mmにした。
これらを半田付けして、ボイラーと仮組してみたのが写真。
本来なら、火室部分と延長部分がピタリと隙間ない状態にならなければならないが、やはり、隙間が・・・・・・(涙)
この形式1060のスクラッチにあたっては、これまででは考えられない程慎重かつ丁寧に工作を進めて来た筈なのに、何故この様な結果になってしまうのだろうか?
2017/02/25
フル・スクラッチ 上回り 形式1060
果たして、上手く位置決めが出来るか心配だったが、心配だからと云って手を拱いて見ている訳にも行かず、兎に角、やって見た。
左右の高さが違うなど何度か失敗したが、何とか半田付けを終了させることが出来た。
火室の側板のボイラーとの接合部分は、予めRを付けているが、それでも段差が目に付くので、半田を盛って整形した。
こうして写真に撮ると、半田の盛り方に粗が見えるが、組み立ててしまえば目に付く部分ではないので、このまゝ先に進むことにする。
2017/02/05
フル・スクラッチ ボイラー 形式1060
念のため食塩水に付けたまゝにしていたボイラーを取り出して、ドリルが折れた個所をチェックすると、まだ何やら黒いものが残っている。そこで、改めて食塩水を作り直し、更にもう一日浸けていた。
そして、もう溶けてなくなった筈と思って、翌日ステンレスのコップを除くと赤錆が見えない。おかしいなぁと思い、再度折れた個所を25倍のピークルーペで見ても、やはり黒いものが・・・・・。
都合3日間も海水浴をさせていたのに、溶けないことがあるのだろうか?
少々、怖かったが恐る恐るピンバイスに咥えた0.6mmのドリルで抉る様にしてみた所、黒いものは刃の溶けカスだった様で、何の抵抗も感じられない。そこで、穴開け作業に移って、無事貫通。
0.5mmの方も同じで問題なく終了させることが出来た。
次の作業は、ボイラーの終端側の処理。
この形式1060のキャブ内にあるボイラーの終端は、垂直に切れておらず、僅かに斜めになっている。当初は、何も考えずに当然の様に垂直に切れている図面を描いていたが、蒸気機関車形式図集Iで少し斜めになっている図を見た以上無視する訳に行かず、それに倣って斜めにすることに変更した。
図面では簡単に斜めに切ることは出来たが、実際に正確に切断するのは少々所か、かなりの難題。正に絵に描いた餅状態。
工作は、出来ればフライス盤を使いたいが、良い素材の固定方法が思い付かず、時間ばかり経っていた。そんな時、フト、材料のパイプをバイスに咥え、そのバイスを更に別のバイスで咥えて角度を付けるのはどうかと思い付いた。
で、早速試して見ると、案外、上手く行きそう。
失敗するのが怖かったが、やらなければ先に進めない。
バイスにパイプを咥えるにも、余りきつく締めるとパイプが変形することもあり得るので、レンチを使わずに手で締めたので、切削の途中でパイプが動いてしまうこともある。そうなっては、元も子もなくなるので、切込み量を0.1mm以下にして、少しずつやって・・・・・・。
何とか、上手く切断出来た(写真では、終端の斜めになった切断面が良く分からないが・・・)
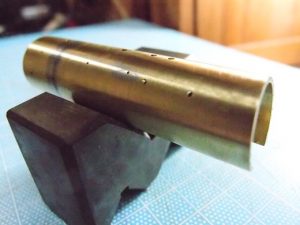
2017/01/31
フル・スクラッチ ボイラー
煙突やハンドレール・ノブなどの位置決め用の冶具を作った所で、早速、穴開け作業に入った。
尚、冶具は穴開けやこれから入る火室部分の切削作業の際、振動でズレてしまうことを防ぐために、ロックタイトで接着している。
で、またもや、やらかしてしまった。
と云うのは、0.6mm、0.5mmのドリルの刃を立て続けに折ってしまった。
実は、0.4mm以上のドリルの刃を折ることは滅多にないことなので、同じ刃を結構長い間使い続けていた。そのために、切れ味が鈍くなっていたのだろう。それに気が付かずに、力を入れ過ぎた結果だろうと思うが、アッと思った時には、パイプに刃が喰い込みピチッ・・・・。
と云う訳で、昨夜、ステンレスのコップに入れた3%の塩水に浸け込んでおいた。
そして、今朝、見たら見事に赤錆がコップの底に溜まっていた。しかし、完全に溶け切ったかどうか判らないので、あと、1日か2日、このまゝ浸けておこうと思う。
2017/01/28
フル・スクラッチ ボイラー 形式1060
ボイラーに固定する煙突や蒸気溜め等のネジ穴の位置決めをどうするか?
色々と考えた末、ボイラーに罫書くことをせずに、フライス盤のXYテーブルを利用してネジ穴の位置を決め、エンドミルで開けることを思い付いた。
そこで、冶具とは云えない簡単なものだが、3mm厚のアルミ板の端材を用いてパイプの内径にピッタリの円盤をML-210で削り出し、その円盤の中心を通る十字線を罫書き、パイプに嵌めこんだ。
そして、フライス盤のXYテーブルに固定したバイスにパイプを咥え、テーブルに立てたスコヤに、この円盤の罫書き線を合わせれば、垂直(Z軸)は確保出来る。
云うまでもないが、X軸、Y軸についてはフライス盤の送りを利用して位置決めをすることになる。
ハンドレール・ノブについても同様で・・・・・・・。
とここまで書いて、又々、ミスをしていることに気が付いた。
写真に写っている円盤上部の水平線は、ハンドレール・ノブ位置(高さ)を示す罫書き線だが、この線も中心を通す必要がある。
つまり、ハンドレール・ノブ用の穴を開ける際は、パイプをぐるりと回転させ、この線を垂直にすることを想定していた。にも拘わらず、罫書くことを忘れていた(大汗)
この状態で改めて中心を通る線を罫書くのは難しいので、冶具を作り直さなければ・・・・・。
尚、実際に冶具の円盤を作る手順は、上に書いた手順とは異なり、十字線の罫書きを先にした上で、その交点を中心にして円盤状に切削した。
(追記)
冶具の作り直しは面倒臭いので、中心線を罫書く良い方法はないかと『円筒 端面 中心線 罫書き』で検索した所、『機械設計のための基礎製図』の第2章にその方法が掲載されていた。
早速、その方法を採用させて頂き、今回は作り直することはせずに済ませた。
« 古い記事
新しい記事 »